Enhancing the Process of Inventory Keeping
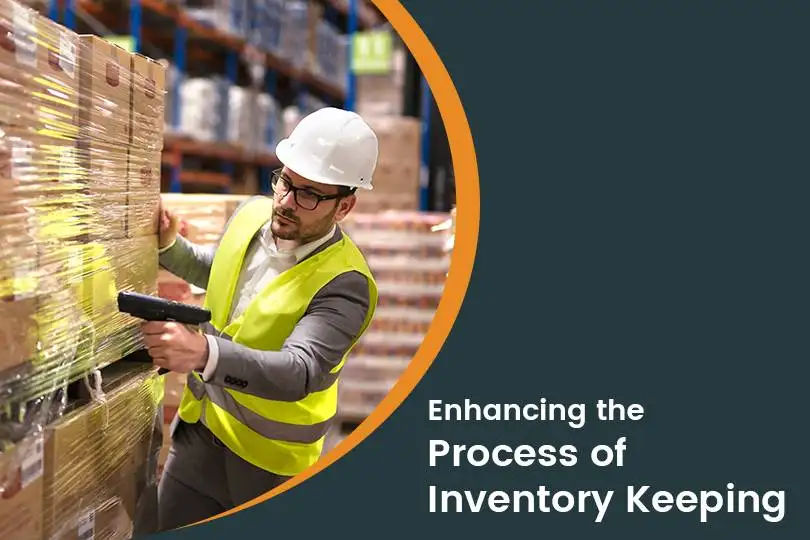
Inventory—most people find this one of the most dreaded aspects of running a business. This is not unusual, given the sheer hassle the task entails. If you are one of those people, if the word itself sounds boring to you, then imagine doing it day in and day out! There is no doubt that a minute and repetitive task like this would annoy anybody. But work is work. And there is no other way, especially when it comes to the service sector.
Ready to get started with Field Promax?
Sign Up FreeLet’s focus on one of the most prominent service sectors, i.e. fire and security companies. When it comes to inventory management, there are some essential factors that come into play specific to this industry. Let’s take a look.
No Importance for Asset Tracking
To begin with, inventory management is not interesting at all. However, not doing it might mean no track of assets. Be it a big company or a small one, whatever assets there may be, one needs to account for them. This helps to avoid the situation of understocking and prevents money wastage.
Due to the sheer disinterest in keeping an inventory, one might lose out on stocks that could be efficiently used otherwise. But understanding the nature of work, the next best option is to make use of software specifically designed for the same, which makes the whole process easy. This will be discussed in more detail towards the end of the blog.
Absence of Vendor Communication Plan
A smooth vendor communication plan requires transparent and accurate inventory levels. However, the reality is probably much different. Companies have specially designed software to address this inefficiency in inventory management.
Let’s look into what happens when there is no such software being employed. Improperly kept inventory would affect vendor communication in the following way. You end up reaching out to the vendor multiple times, back and forth, because you are not sure about the exact requirements. Now this miscommunication might cost you more than anticipated.
On the other hand, regular and Effective Communication with the vendor would keep them informed about the requirements from time to time. This would help them, in turn, to help you with inventory forecasts as well.
Absence of Inventory Accountability
For a small company, with a small inventory and team members, the easiest way out is to maintain check-in and check-out sheets. These can be then put into spreadsheets, and the work is done. It seems easy and free. So, why not? Now imagine the case when the company has grown in size. This means more room for not just proper storage, but for the growing team too. A couple of misplaced items and forgotten check-out sheets can turn your inventory system upside down in no time.
This is where the lack of accountability poses a problem. When the situation goes out of control, even then one might fix it. There is no way the source could be found, or such a situation can be prevented from happening again.
On the other side, with Fire and Security Management Software, every action is fed into the system with a person’s name, thus, helping to track the root cause.
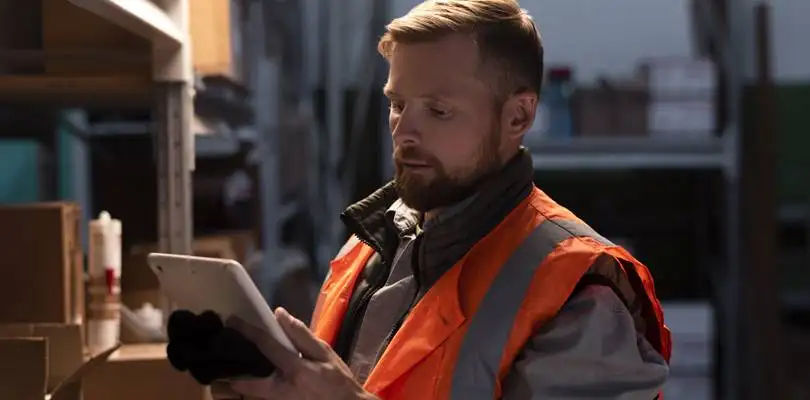
Inaccurate Inventory Forecast Method
Inventory forecasts are made based on these previously mentioned spreadsheets. Now with the scenarios explained above, there is a great possibility that the spreadsheet contains incorrect information. Next, comes out is the forecast which follows the pattern and sets the incorrect order for the stock needed. The understock situation continues to exist. The whole purpose of the inventory forecast goes in vain.
To fix this situation with the existing methods, one would need to go through the incorrect spreadsheets and look for the error. In any real-time situation, this is highly unlikely because of the sheer lack of time. Things get busy, and this means that there’s only a little time to spare for a thorough inspection.
Want a personalized demo?
See how Field Promax can transform your field operations
Overstock and Understock at the Same Time
One of the employees happens to leave the equipment in the car and forgets to return it. The next day it’s someone else, and this goes on for a couple of days till the equipment is no longer there for usage. For the manager, it means the tool ran out of stock and gets another bunch, only to find the employees got them back, all at once.
An overstock wouldn’t seem bad, but for space and money wasted over it. Had there been a fire and security software in place, the same money spent on that tool could instead be put into a good which was running out.
The same situation can be used to explain the understock aspect, which was the source for all this. Now, what happened, in this case, is nothing intentional but a simple error due to the situation during work. It is something that can happen to anybody.
Inefficient Employees Managing Inventory
Any change is not acceptable well when it is bought. This applies to all situations. When talking about an organization, it applies all the more. From the employee perspective, it would mean changing to new work methodologies. Now when there is no proper training given for the same, it might not be an easy task. Thus, the execution lags and what was brought to improve the condition leaves things worse.
Computer Weekly reports that fear of change dominated the staff that confronted the new software. At the same time, “the biggest challenge businesses face in digital transformation is issues around culture and bringing people on the way.” Hence, proper training is key. High-quality training can help improve the hesitation posed by the employees and thereby, smoothening employee-employer relations as well.
So before bringing in a highly efficient fire and security work order management software discussed with the employees and walk them through the process. This way, they will co-operate better, having understood the motive behind such a change.
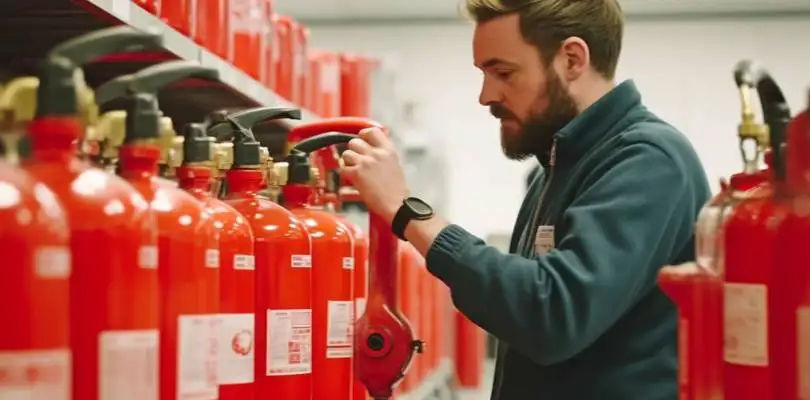
Understanding Inventory Management Software for the Fire and Security Industry
Until this point, we hope to help you realize the drawbacks you might face if you are not using inventory management software for your fire and security business. With that said, the obvious question that would follow is, “What is inventory management software, and how does it help fire and security businesses?”
Let us try to understand the essentials. Inventory management software tailored for the fire and security industry is a specialized solution designed to streamline and optimize the handling of equipment, devices, and components related to fire protection and security systems. This software is crafted to meet the unique needs and challenges of businesses operating in this sector, where precise inventory control is paramount for ensuring the functionality and reliability of safety and security systems. Inventory management software in the fire and security industry allows organizations to track the availability, usage, and status of various components such as fire alarms, surveillance cameras, access control systems, sensors, and other essential devices.
Key features of inventory management software for the fire and security industry include real-time tracking of stock levels, monitoring expiration dates for perishable items like batteries or sensors, and managing equipment across multiple locations. This software enables businesses to maintain accurate records of their inventory, helping prevent stockouts, reduce excess stock, and optimize ordering processes. It also aids in compliance with industry regulations by ensuring that safety equipment is regularly inspected, maintained, and replaced when necessary. Ultimately, inventory management software for the fire and security industry plays a crucial role in enhancing operational efficiency, minimizing downtime, and ensuring that organizations can deliver reliable and compliant safety and security solutions to their clients.
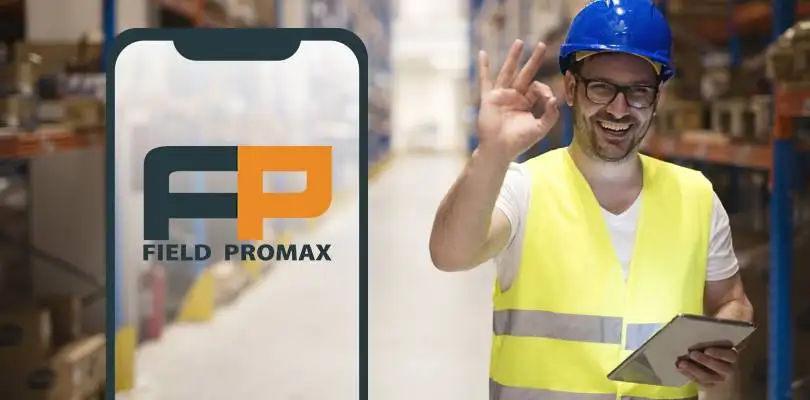
Benefits of Inventory Management Software for Fire and Security Businesses
Optimized Stock Levels
Inventory management software enables fire and security businesses to maintain optimal stock levels. By tracking usage patterns and demand fluctuations, the software ensures that essential components, such as fire alarms or security cameras, are neither overstocked nor understocked. This prevents unnecessary costs associated with excess inventory and ensures that critical items are always available.
Real-Time Tracking
The software provides real-time visibility into inventory levels and movement. This instantaneous tracking capability allows businesses to make informed decisions promptly, addressing issues like low stock or identifying fast-moving items. Real-time tracking enhances overall operational efficiency by reducing delays and improving responsiveness to changes in demand.
Enhanced Accuracy and Precision
Automated data entry and barcode scanning features in inventory management software significantly reduce the likelihood of human errors. This heightened accuracy ensures that businesses maintain reliable records of their inventory, preventing discrepancies that could lead to operational disruptions or financial losses.
Streamlined Order Management
Efficient order processing is facilitated through inventory management software, which automates and streamlines the ordering process. Businesses can set up reorder points and receive alerts when stocks fall below predefined thresholds, ensuring that replenishment orders are placed in a timely manner to avoid stockouts.
Improved Cost Control
By preventing overstock situations and minimizing the risk of stockouts, inventory management software contributes to better cost control. Businesses can optimize their purchasing strategies, negotiate favorable terms with suppliers, and minimize holding costs associated with excess or obsolete inventory.
Compliance Management
For fire and security businesses, compliance with industry regulations is crucial. Inventory management software helps ensure that safety and security equipment are regularly inspected, maintained, and replaced as needed. This adherence to compliance standards not only ensures the safety of end-users but also protects the business from regulatory penalties.
Efficient Batch and Expiry Management
Some inventory items, such as batteries or sensors, may have expiration dates or require batch tracking. Inventory management software allows businesses to monitor these details closely, ensuring that expired or outdated items are promptly removed from inventory. This feature is particularly critical in maintaining the functionality and reliability of safety and security systems.
Increased Productivity
Automation of routine tasks, such as data entry, stock tracking, and order processing, frees up valuable time for employees. With inventory management software handling these manual processes, staff can focus on more strategic activities, leading to increased productivity across various aspects of the business.
Accurate Financial Reporting
Inventory management software provides accurate and up-to-date data on the value of inventory. This information is crucial for financial reporting and decision-making. Businesses can generate precise reports on inventory valuation, turnover rates, and other financial metrics, supporting strategic planning and analysis.
Enhanced Customer Service
With the ability to quickly fulfill orders, accurately track shipments, and provide real-time information on product availability, inventory management software contributes to enhanced customer service. Businesses can meet customer demands promptly, resulting in increased satisfaction and loyalty.
Conclusion
Implementing software might not sound like the easiest thing, but it’s the only way to tackle all these challenges and many others that come with big contracts. So, don’t waste any more time. Switch to an advanced software solution to take care of your inventory. And your best bet in this regard is Field Promax, without a doubt!
The software offers the following features:
- Elimination of the possibility of understock.
- Reduce excess stock through efficient inventory control.
- Avoiding misplacement or damage to tools, thus draining your resources.
For more information, contact Field Promax
We're here to help you get started