Why Your Manufacturing Business Needs a Field Service Management Software

In today’s fast-paced manufacturing world, staying ahead means solving problems quickly and planning for the future. Field Service Management (FSM) software is a powerful tool that can help with both. And it’s growing fast. In 2022, the FSM market was worth $3.83 billion. By 2028, it’s expected to reach $7.16 billion. That’s 11% growth each year!
Why this rapid growth? More businesses want cloud-based solutions. They’re also using mobile devices more. This helps them see data quickly and work better. For FSM tech, the future is here now.
Let’s explore why your manufacturing business should consider implementing a field service management system as part of its Enterprise Resource Planning (ERP), and how it can solve common challenges while preparing you for Industry 4.0.
How FSM Solves Key Manufacturing Challenges
1. Better Coordination on the Factory Floor
Problem: Poor coordination between production lines and maintenance teams can lead to costly downtime in manufacturing.
How FSM Helps:
- Connects factory floor managers with maintenance teams via mobile apps
- Allows quick assignment of technicians to urgent machine breakdowns
- Gives maintenance staff instant access to equipment specs and repair histories
- Enables real-time updates on repair progress, visible to all relevant staff
- Sends automated alerts about machine issues to prevent unexpected shutdowns
- Keeps production and maintenance teams in sync, reducing response times
- Minimizes production line downtime with faster, more efficient repairs
- Puts critical manufacturing data at everyone’s fingertips
2. Enhancing Equipment Tracking
Problem: Poor equipment management leads to inefficiencies and unexpected downtimes.
How FSM Helps:
- Provides real-time visibility of equipment location and status
- Maintains detailed service histories for each piece of equipment
- Tracks equipment utilization rates and performance metrics
- Facilitates quick identification of underutilized or problematic equipment
- Supports better decision-making for equipment allocation and replacement
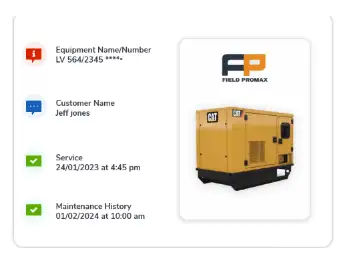
3. Enhancing Workforce Productivity
Problem: Workorder management is difficult because of complex workflow
How FSM Helps:
- Automates scheduling based on skill sets and job requirements
- Provides mobile access to technical documentation and SOPs
- Captures time and attendance data for accurate labor tracking
- dentifies training needs based on job performance metrics
4. Improving Quality Control Processes
Problem: Poor quality can cost up to 20% of a company’s revenue.
How FSM Helps:
- Implements digital checklists for standardized quality inspections
- Captures and analyzes quality data in real-time
- Facilitates quick issue reporting and resolution tracking
- Generates comprehensive reports for compliance and audits
5. Boosting Customer Satisfaction
Problem: 65% of customers expect faster service than they did 5 years ago.
How FSM Helps:
- Enables faster response to customer service requests
- Provides accurate ETAs based on real-time technician locations
- Facilitates easy sharing of service reports and invoices
- Collects and analyzes customer feedback for continuous improvement
6. Enhancing Asset Performance
Problem: Poor equipment management can reduce productivity by 5-20%.
How FSM Helps:
- Schedules preventive maintenance based on usage or time intervals
- Tracks asset performance metrics and downtime reasons
- Calculates asset ROI and total cost of ownership
- Supports data-driven decisions on equipment replacement or upgrades
7. Ensuring Regulatory Compliance
Problem: Non-compliance can result in hefty fines and damage to reputation.
How FSM Helps:
- Maintains detailed service logs for all equipment
- Ensures adherence to maintenance schedules and safety protocols
- Provides easily accessible records for inspections and audits
- Tracks certifications and training requirements for technicians
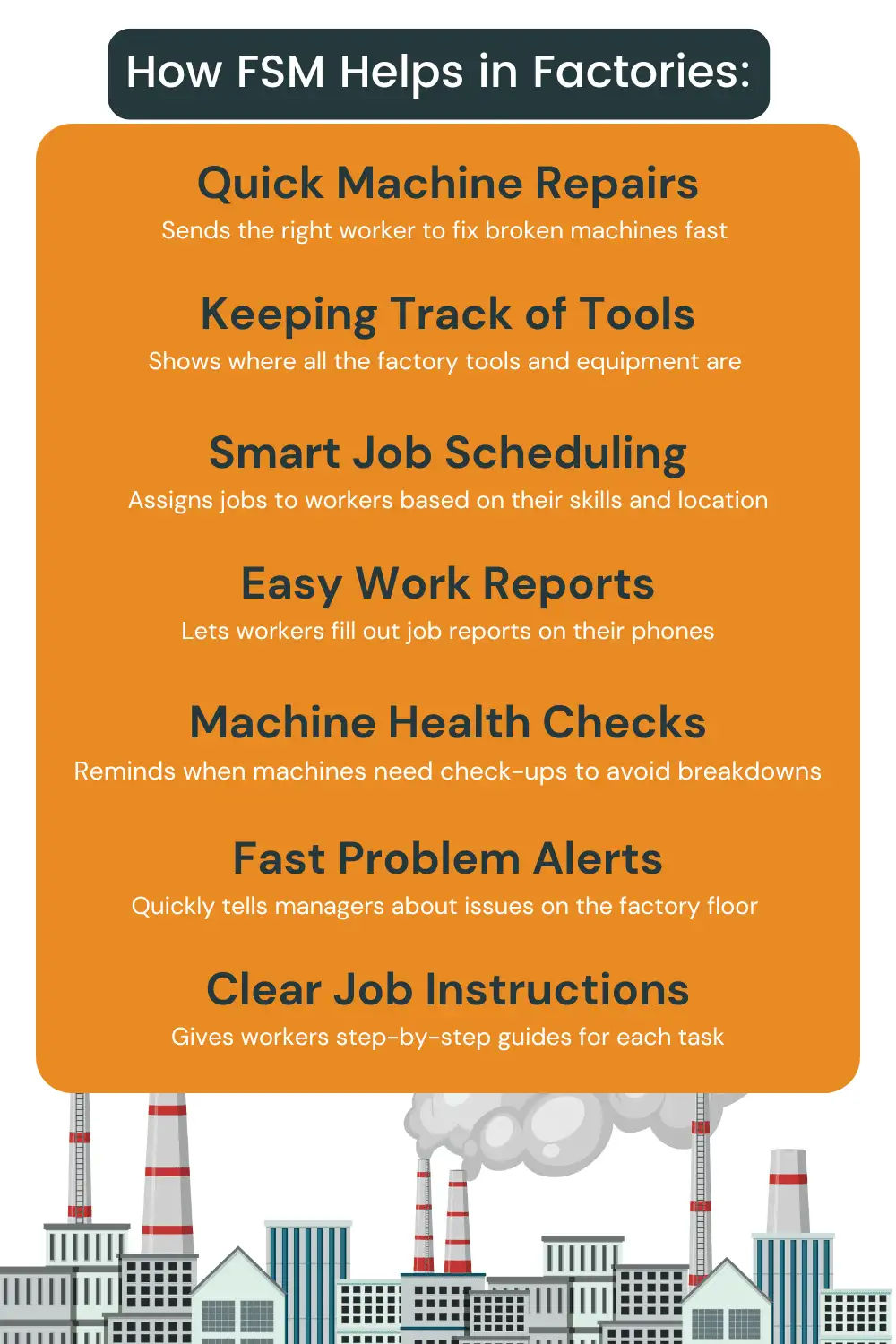
FSM: Your Stepping Stone to Industry 4.0
FSM isn’t just about solving today’s problems. It can also help you prepare for the future of manufacturing, known as Industry 4.0. Here’s what you can expect in the near future:
1. Connecting Machines (Internet of Things)
- FSM can collect and analyze data from sensors on your equipment
- This helps predict when maintenance is needed and monitor performance in real-time
2. Creating Digital Twins
- FSM’s detailed equipment tracking can help create virtual copies of your machines
- These digital twins let you test and optimize processes without disrupting production
3. Using Artificial Intelligence
- The data FSM collects can feed AI systems
- AI can predict equipment failures, optimize maintenance schedules, and suggest improvements
4. Implementing Augmented Reality
- Advanced FSM can use augmented reality to help with repairs
- Technicians can see repair instructions overlaid on the actual equipment
5. Enhancing Supply Chain Transparency
- FSM can be a first step in using blockchain in your supply chain
- Start by securing maintenance records and verifying the parts’ authenticity
6. Processing Data Closer to the Source
- FSM can use edge computing to process data near where it’s created
- This speeds up critical operations and saves on data transfer costs
Getting Started with FSM
While FSM offers many benefits, implementing it requires careful planning:
- Look at your current processes and identify areas for improvement
- Choose FSM software that works with your existing systems example Quickbooks
- Plan how you’ll move your data and keep it secure
- Train your team thoroughly to ensure they use the new system
- Start small with a pilot program and grow from there
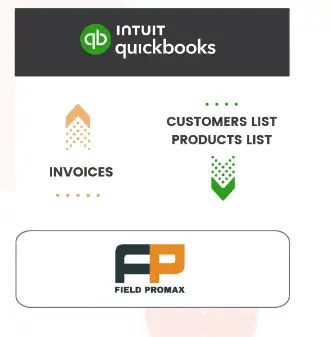
Conclusion
As manufacturing continues to evolve, FSM software is becoming a must-have tool. It solves today’s challenges while preparing you for tomorrow’s technology. By improving equipment uptime, optimizing resources, enhancing quality control, and providing data-driven insights, FSM can significantly boost your manufacturing operations.
The rapid growth shows how valuable FSM is becoming for businesses like yours. By addressing specific manufacturing challenges and paving the way for Industry 4.0, FSM software can help you stay competitive in an increasingly technology-driven industry.
Don’t get left behind. Consider how FSM can transform your manufacturing business, solve your current problems, and set you up for future success. The future of manufacturing is here, and FSM is your ticket to being part of it.