The Ultimate Guide to Job Cost Sheets: How to Track Job Costs and Improve Profitability
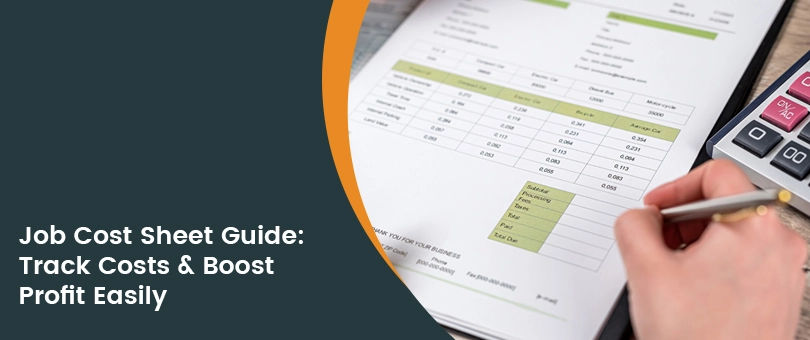
In Q3 2024, labor costs in U.S. manufacturing jumped 5.3% – yep, according to the Bureau of Labor Statistics. If you’re not job costing right, those rising costs won’t just dent your margin – they’ll bulldoze it.
Tracking job costs sounds as thrilling as watching a paint dry. Yet, here you are, trying to make sense of a job cost sheet, like it’s going to save your business from bankruptcy.
So, what is a job cost sheet exactly? Is it a glorified Excel sheet, or is it the magic wand that turns the chaos into profit? A job cost sheet is your backstage pass to understanding where your money goes during the project.
Whether it’s material costs, labor or that one subcontractor job who somehow charges double for showing up late.
In this guide, we will drag you through the trenches of job cost sheet templates, reveal all the dark art of tracking job costs and a monumental concept of profitability. By the end, you’ll either be a job cost sheet wizard or curse your day for running a business.
Ready to get started with Field Promax?
Sign Up FreeWhat is a Job Cost Sheet?
It’s definition time! A job cost sheet is a detailed document recording every dollar spent on the specific project. It is like a nosy neighbor who notes every move you make- except it’s actually helpful.
Unlike general accounting it records that lump every time something happens, any sad expenses, or any unexpected ones. A job cost sheet lets you see costs at the micro level. Who uses them? Oh, just your friendly neighborhood construction companies, contractors and manufacturing firms who are tired of watching their profits disappear.
Imagine you’re a contractor bidding for a renovation project. Your budget is $20000, but thanks to the job cost sheet, you realize that your crew has the talent for burning through materials like they’re free samples.
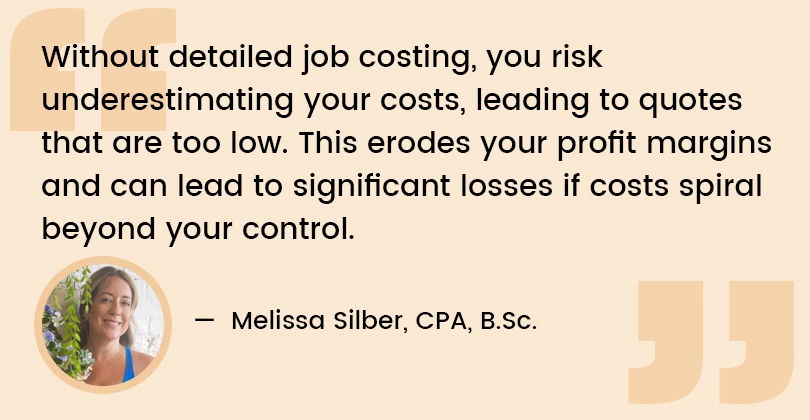
Why Are Job Cost Sheets Important?
Why bother with a job cost sheet when you can just keep winging it and hope for the best? Because ignorance may be a bliss, but it is also expensive. Here’s, why job cost sheet matters:
- Complete cost visibility- Instead of pretending you know where your money goes, a job cost sheet throws it all out in the open- material, labor, overhead and all other surprise business expenses.
- Preventing cost overruns- Without a job cost sheet template, you are likely to experience those “Wait, who spent that much on a mop?” moments. Track everything in real-time and save yourself from hyperventilating situations.
- Accurate pricing- Want to stop underbidding jobs, and digging your own financial grave? Use past job cost sheet data to set realistic, profitable rates.
- Profitability analysis- If your idea of a profit margin is “Whatever’s left over,” then congratulations, you need a job cost sheet more than anyone. It helps you measure if you’re making money or just burning it.
- Data-driven decision-making- Yes, it sounds like corporate jargon but reviewing job cost sheets for trends can improve your decision-making. Maybe you’ll finally figure out that hiring your cousin isn’t a great idea.

Key Components of a Job Cost Sheet
Alright, folks! Now it’s time to break down the chaos of job costs with a pinch of sarcasm and a side of reality? Let’s dive into the key components of a job cost sheet- that magical document standing between you and a financial facepalm.
A. Job/Project Details
First up, the job/project details- basically it’s your way of proving that you actually know what you’re doing. A job cost sheet includes:
Job number/name- So when management says, “What’s this expense is for?” you should not respond it with, “Uh, I don’t remember”
Client details- Just in case they forget they hired you.
Start and end date- To confirm that the ‘end date’ isn’t just about wishful thinking.
Budget estimate vs actual cost comparison- Because seeing how far off your estimates are is always a confidence booster.
B. Direct Materials
Ah, materials, that’s a lot to consider- the stuff that somehow costs triple to what you thought it would. What counts as direct materials on a job sheet? Let’s see
Anything used up during the job- wood, steel, tears of frustration.
Record material usage and costs in real time, or just pray you remember it later.
Example- For a construction project, if you have estimated 100 bricks and end up needing 200, congratulations! You’re officially over budget.
C. Direct Labor
Tracking labor is like herding cats, except the cats want overtime.
Track labor hours and wages honestly- no, Tom, your 2-hour lunch break doesn’t count.
Account for the overtime, rental costs and those mysterious “coffee breaks.”
Why does it matter? Labor costs impact profitability more than you think, especially when your workers think “flexible hours” means “showing up whenever their heart says.”
D. Equipment Costs
Your equipment isn’t just lying around waiting for a spa day. There are costs that will cut your pocket if not administered properly:
Rental fees, fuel, depreciation- they all add up, buddy!
Allocate equipment costs to a job when it actually gets used. That idle bulldozer? Not free, add it.
Example- Tracking machinery usage on a job cost sheet helps ensure that a backhoe that dug one hole didn’t cost you a kidney.
E. Overhead Costs
Overhead- aka the “invisible” costs that still demand a cut. What is overhead? The lights, the A/C, the snacks in the break room- all of these things keep your crew from revolting. Allocate all the consumed overhead using fancy methods like “percentage of labor cost” or just a wild guess. Common categories should be included like: admin salaries, insurance, and coffee (it’s obvious that no one works without a coffee.)
F. Subcontractor Costs
Subcontractors are professionals that bring in some light to your day when you need them the most.
Include subcontractors’ expense in the sheet if they actually worked for you- not if they ghosted you halfway through.
Categorize all the payments to know if you are paying for the real experience or “my cousin knows plumbing.”
Make sure your outsourcing doesn’t eat into your profit margins- unless it’s worth the sanity.
G. Total Cost Summary
This is the moment of truth for you. How much did you actually spend versus what you planned? Spoiler alert- it’s probably going to be more.
Add up all these cost categories. If the total cost doesn’t make you want to lie down, congrats, you won the race.
If applicable, calculate cost per unit to see if you priced things like a genius or a fool.
Go for budgeted vs. actual cost analysis- because it’s always going to blast to see how wrong you were.
How to Create a Job Cost Sheet (Step-by-Step Guide)
-
Gather all job details- To start with Job sheet creation, start calculating like a caffeinated accountant. But, before calculating know what is a job cost sheet and what it should include. A job cost sheet has essential details like job number, client information, project description and timeline. If you’re someone with extra organized skills, you might even use a job cost sheet template. Spoiler alert- it won’t magically fill itself, so get your hands in.
-
Track material costs in real time– Ever thought why your “estimated” material cost was a cute little lie? Well, tracking material costs in real time can help you avoid that awkward conversation with your bosses about why the budget is blown on the face. List all the material, and their relevant costs- no you cannot skip that tiny screw, account it also.
-
Record labor hours and wages- This part is actual fun- for everyone but the payroll department. Record who worked, how long they worked and how much are they paying them to work. If Thomson is taking three coffee breaks during his shifts, that’s between his conscience. But make sure you accurately log labor hours and wages to get into precise job costs.
-
Log equipment usage and costs- Your shiny equipment isn’t running on hopes and dreams. Track its usage and any other cost associated with it. If you rented a bulldozer to dig a small trench, it’s time to face the fact that it will cost more than just a shovel- but also less back pain.
-
Allocate overhead expenses- Overhead expenses come into the “miscellaneous” section that will test your creativity. Utilities, office rent, toilet paper and insurance for the break room- you name it. They’re sneaky ones, but they add up and if your job cost sheet ignores them, so will your profitability.
-
Add subcontractor charges- Got a subcontractor that can do the job you pretended to know how to do? Great! Just remember to add their charges to the cost sheet and understand subcontractors aren’t free consultants.
-
Calculate total job cost- Now, do some math. Add all the material cost, labor, equipment, overhead and subcontractor charges. You have the total job cost- voila! If this number makes you want to lie down for a bit, congratulations, you did it all right!
-
Compare actual vs. estimated costs- Brace yourself for a reality check now. Compare your prepared actual job cost sheet to the estimated one. If they match, go enjoy a movie because you clearly have some supernatural powers to do it one go. If not, well, it’s time to figure out why.
-
Review and finalize the cost sheet- Before you file this masterpiece, review the job cost sheet template you used. Make sure every cost has been accounted for. If you missed any category, just add it before someone else notices. And, there you go- a job cost sheet that actually makes sense and doesn’t double as a piece of modern art.

Job Cost Sheet Example & Template
Want a personalized demo?
See how Field Promax can transform your field operations
Alright, let’s get into practicality! Here’s a peek into job costs that’s not just a bunch of boring columns but an actual tool that you might find useful! (gasp!)
Real world example- Imagine a construction project where everything goes wrong- surprise, surprise! You estimated $8000 for materials, but it costs $12000 because Smit ordered premium Italian tiles instead of the basics. Labor? You budgeted $12000, but Karen needed triple overtime. Equipment rental? Oh, that idle excavator? Yep, $5000. In the end, the total goes over the estimates. Welcome to reality!
Sample template format- Your standard job cost sheet template usually has the columns like job details, labor, equipment, overhead, subcontractors and total costs. Add a comparison column for estimated vs. actual cost there to visibly cringe at your miscalculations.
How to Calculate A Job Cost Sheet
Job cost sheets are calculated using the following steps:
Step 1: Put together all the materials costs needed to finish the job
Step 2: Determine the cost of direct labor
Step 3: Determine the operating and overhead costs.
Step 4: Add up all the expenses incurred in steps 1 through
If you are working on a job order that requires multiple projects, you can calculate the total cost individually or divide the total cost by the number of projects to determine the total cost.
Best Practices for Using Job Cost Sheets Effectively
so, if you want to be a responsible adult about this, here’s how to use a job cost sheet without turning it into a disaster:
-
Update it regularly- Yes, that means more often than “whenever I feel like it.” Ideally this means daily updates about the client to ensure nothing slips through the cracks. Trust me, playing Sherlock to find out why you overspent isn’t fun.
-
Keep invoices and receipts organized- No, your car’s glove box is not a filing system. Get a folder, or a digital system that stores your entire invoices and receipt. Lost invoices = Lost profits.
-
Train your team- Because if Scott still thinks her lunch break is billable, we have a huge problem. Teach them the art of accurate time-tracking and cost recording- it might just save your sanity.
-
Refine future estimates- Use past mistakes- sorry, learning experiences- to make more perfect estimates. If Jerry’s “premium taste” for material always sinks your budget, plan for it!
-
Leverage software- Why not use technology for heavy lifting? An Excel job cost sheet template works, but a software specializes in it and helps avoid “accidental” triple-time wages, misfiled expenses and tantrums over data loss.
Frequently Asked Questions (FAQs) about Job Cost Sheets
Should I fill out a job cost sheet during or after the project?
Well, unless you have a time machine to go back and forth, it’s better to record it immediately. Filling it out after it happens results in missing receipts, forgotten details and series of unwanted conversations. Track it down live; your future self will thank you.
Can I create a job cost sheet in Excel, or do I need software?
You can use Excel if you enjoy endless scrolling, broken formulas and risk of deleting the entire cost history with one wrong click. But hey, if you want to keep your sanity alive, use specialized software. Bonus- Some even offer a ready-made job cost sheet template to save your time.
How is a job cost sheet different from a cost estimate?
A cost estimate is your optimistic guess before the chaos; a job cost sheet is the ugly truth that smacks the reality out of you. think of it as the “Before and After” meme of the project budgeting.
Who should be responsible for maintaining the job cost sheet?
Ideally, someone who can count, follow instructions and won’t “accidently” expense their lunch every day. This can be a project manager (managing overall Project), an accountant or an office manager- just not Mr. X, who thinks “miscellaneous” means “my weekend getaway.”
For more information, contact Field Promax
We're here to help you get started
Conclusion
Why actually bother with a job cost sheet? Well, unless you like being over budget and underpaid, tracking cost is crucial. It’s not just about dodging losses- it is more about improving profitability and understanding where your money goes.
By tracking costs, you’re not just filling out a job cost sheet template, you’re setting yourself up for better financial control, less hassle and maybe, a pat on the back for staying on budget.
Now go back, track costs, and resist throwing the sheet out of the window.